The rise of digital technology and IoT in recent years opened up many opportunities for companies. Namely, opportunities to innovate, streamline operations and invest in proactive maintenance strategies.
Regardless of your industry, moving from a reactive to a proactive mindset is simply good business sense. With a reactive approach, you’re left scrambling if something suddenly breaks, and waiting on lengthy shipping times due to the supply chain crisis. While we’ve already circumvented some of these issues for our clients by fully designing and manufacturing our entire product line in North America, there are still areas where companies can become more proactive.
Over the last decade, we have been hearing about “Industry 4.0”, the Internet of Things (IoT), and interconnectivity. When IoT came to exist, it took two to three years to unwind its potential and usage.
At Interceptor, we believe one of these key strategies is predictive asset maintenance (PAM).
Why Predictive Maintenance is the Future of Modular Solutions
Predictive maintenance, a consequence of “Industry 4.0” and IoT, is a process that uses historical data to forecast when equipment is likely to fail. It is loaded with data collection and preprocessing, early fault detection, fault detection, time-to-failure prediction, maintenance scheduling, and resource optimization.
It can help solve issues such as:
- Production lags or downtime
- Inaccurate production capacity or not enough volume to meet demand
- inaccurate maintenance costs
- Service shutdowns that occur too late or too soon
- A lack of foresight into future issues
How Predictive Asset Maintenance Can Manage Scheduling and Downtime
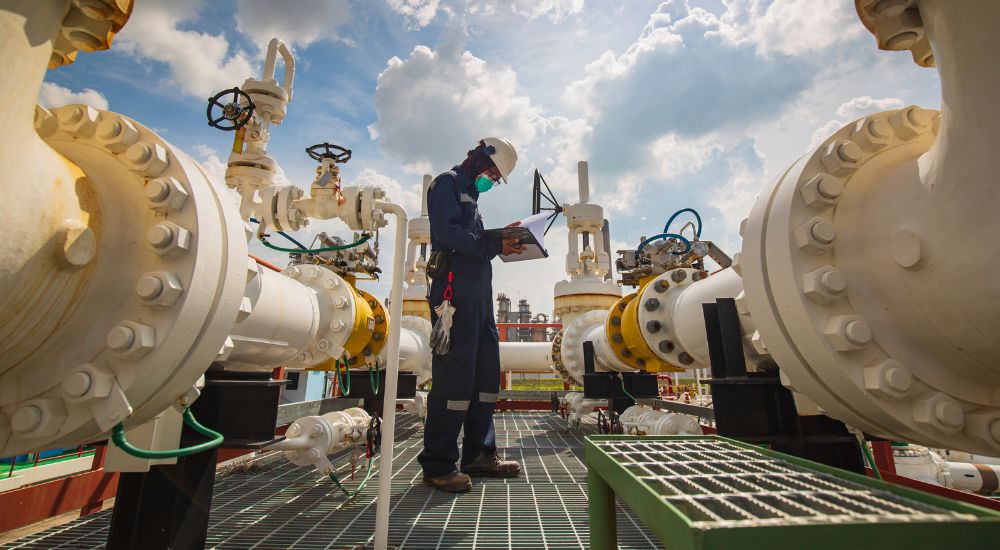
According to research by Deloitte, predictive maintenance can “reduce the time spent on maintenance planning by 20-50%, increase the efficient and effective utilization of machinery and equipment by 10-20%, and reduce total maintenance costs by 5-10%.”
Scheduling is a big part of predictive maintenance, as it can help you align maintenance with known downtime. For example, if you know your company will be out over Christmas, you can close down your operations when everyone is gone and begin reopening when you’re ready. Or, you can choose to run your operations at 75% and potentially get extra months out of your machinery. This saves you time, energy, and—ultimately—money.
Industries That Could Benefit from PAM
Predictive maintenance in oil and gas industries can help companies assess the health and performance of equipment in real-time, and schedule maintenance when any issue is detected before it becomes a crisis. Strategically placed modules can help equipment withstand rugged industrial conditions or adverse weather events, and report back to maintenance workers to track any potential problems.
A strong PAM solution has the capacity to prevent disasters like the Deepwater Horizon Oil Spill of 2010. This spill revealed a lack of visibility in remote, offshore locations and emphasizes the critical importance of constant monitoring and increased visibility in oil and gas.
PAM can also positively impact things like water usage and utility bills in any industry that owns office space or working facilities like in manufacturing. Most of the time, it isn’t until the end of a billing cycle that utility companies identify a potential concern. They rely on a stark increase in cost to tell them if there is a potential inefficiency or leak. With predictive maintenance, instead of waiting for that monthly billing cycle to bring your attention to a leaky pipe, there are data triggers that continuously track data, comparing it to historical data and KPIs. If the numbers began to climb, these triggers set maintenance into motion.
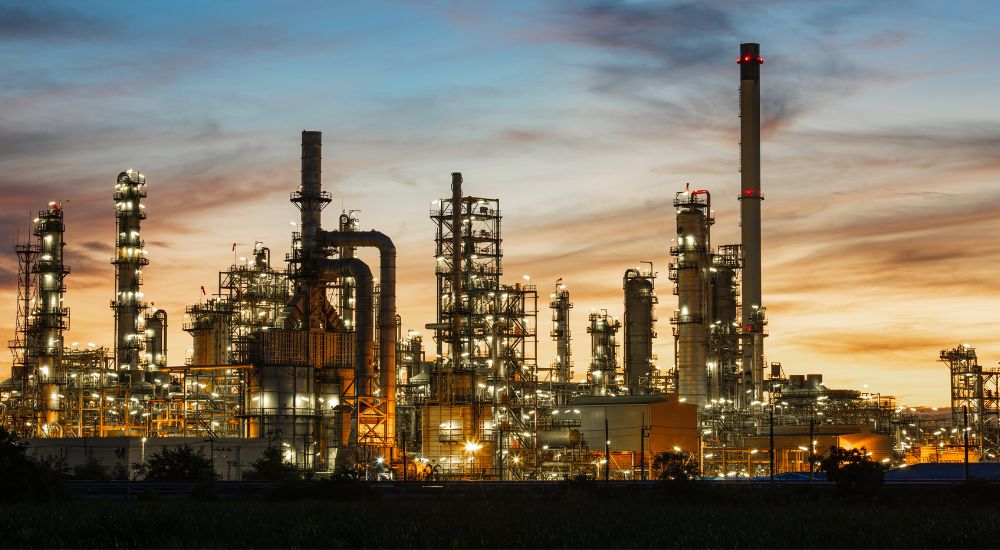
Several companies offer software packages that say they offer predictive asset maintenance, but none of them offer complete hardware integration. This means their predictive asset management solutions are really just data analytic software. That isn’t to say these software solutions aren’t incredibly useful, they simply still require human insights to make decisions and set maintenance into action.
For true predictive asset maintenance to exist, it must go beyond gathering information that helps humans take action and move into the technology itself performing those necessary actions. The tech should both identify the maintenance needed and manage it. As we continue to innovate in the modular solutions space, we look forward to other companies grasping hold of true predictive management capabilities, and in the future, we hope to share some of our own solutions.
Subscribe to our newsletter and stay up to date on our latest offerings and innovations.